We had to find the nap, to create the nap. But then through the processes of being wet and dried, the nap was flat, like that table top, so Steve had to bring the nap back up again.
[Reg, Morlands]
There was four of us in the line. So we started with the first one, the skin that was filthy dirty. Put it in, put it through the mangle, put it through the mangle again, through the water, three or four times. It went down the line. Then at the end, it were pretty good. We did that for about six or seven hours a day! It was quite hard work.
[Terry, Baily’s]
There were about three boilers – they supplied the steam which is the lifeblood of the factory. Every department had a steam pipe of some description for heating or powering something.
[Adrian, Morlands]
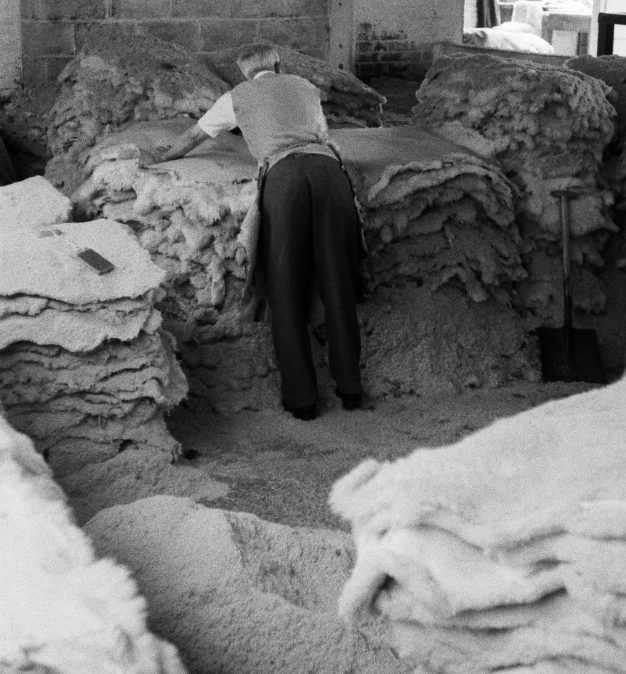
Photo: John Morland
Cos you’ve got a spinning wheel and he’s pulling, so you’ve got to hold the skin against a board, and then you’ve got to lie over the wheel and press all round the neck and round the flanks. When you’ve done that you’ve got to catch hold of the skin and go over the whole wheel. And then you turn it round and you do the other side.
[Reg, Morlands]
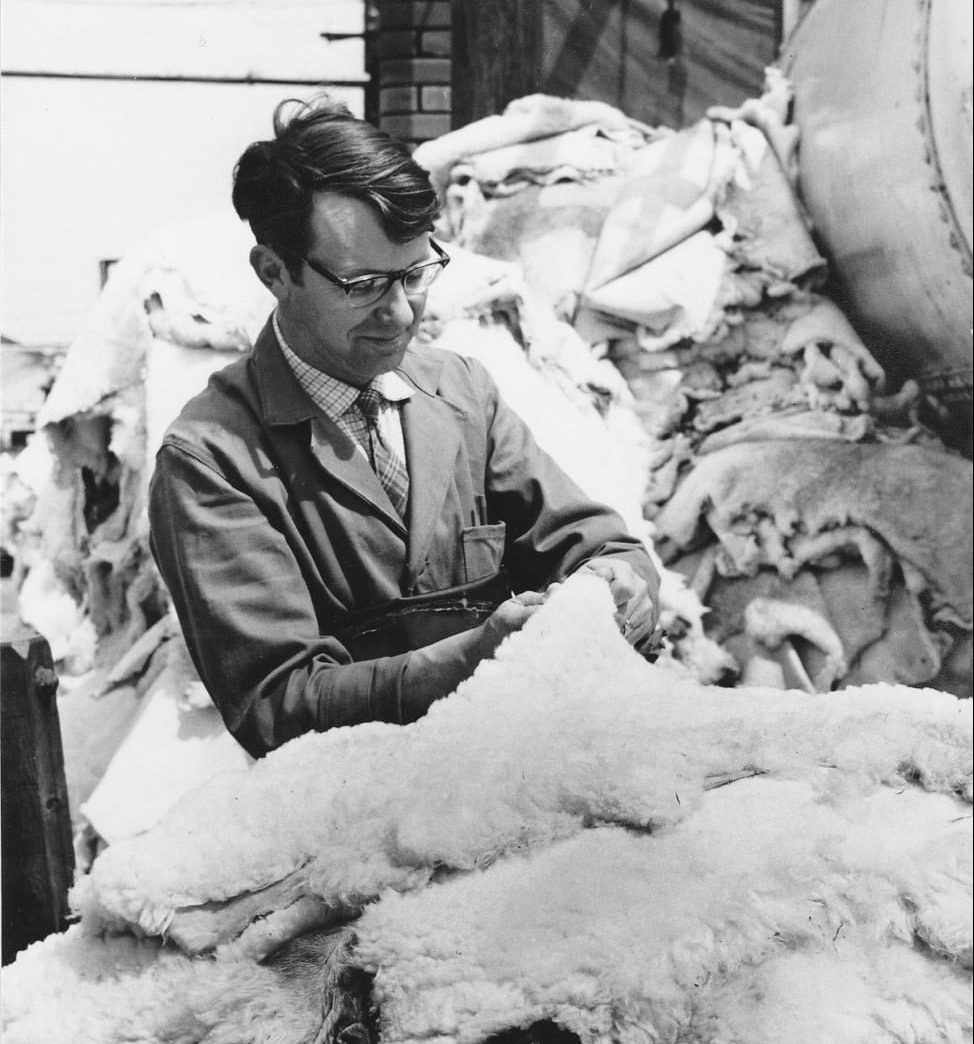
Photo: Jane Laver
I graded the skins, and we decided whether they were going in for linings of boots, or sockers – the bottom of the boot – or whether they should be used for something else. Because we used to make lots of other things – paint rollers, powder puffs, car seat covers, various things. Powder puffs were the merino wool, quite fine wool from South Africa.
[Roger, Morlands]